Our Mechanical Design Team places emphasis on following design elements.
- Cooperation with the ID designer (Maintain size, product performance and layouts without losing its conceptual images.)
- Productivity
- Ease of disassembly
- For Mold tooling and forming conformability
- Usability
- Liability
- Noise suppression (ESD, EMC, Noise sound)
Designable Components
- Plastic mold components
- Rubber and elastomer components
- Metal stamping components
- Non-ferrous metal components (ex. aluminum)
- Die-cast metal components
Designing Process
ID Design Adjustments | We study the ID design data and work closely with the ID designer to tune it up, adjusting parts layout, features, durability, material choice and secondary processes, yet keeping the design faithful to customer’s original concepts. |
---|---|
![]() |
|
Product detail Design | Following consultation with ID designer for design adjustments, our next step is drawing out detail designs; laying out structural, mechanical and electronic parts using 3D CAD. We draw the designs to qualify desired product specs and quality specs from our customer.
Output |
![]() |
|
Prototype Trial | We handle handmade subcontractor and issue order to make prototype parts. Upon receiving the parts we assemble them into a prototype of a product and inspect its quality. At this stage we identify any current and possible issues and make design revisions to solve them before moving on to metal mold making.
Output |
![]() |
|
Making Tooling | We consult with tooling suppliers about its structures discussing in details about each parts with 3D data and parts drawings. This important step further prevents tooling issues and leads to smooth prototype making. |
![]() |
|
Attendance tooling & injection (forming) maker for test shots | After tooling are made, we attend to tooling tries at part suppliers to check if the parts are coming out in desired sizes and shapes, and inspect for any tooling defects. |
![]() |
|
Trial production samples DVT | Once development of all the components and PCB are completed, we assemble samples and perform an inspection. At this stage, all problems detected from individual parts, assembly, and quality test inspection are closely studied. We carefully detect the problem causes and perform necessary countermeasures. We notify the parts suppliers for any part design revisions and improve on whole quality of the product.
Output |
![]() |
|
Tooling, Parts approval | After solving the issues detected in production trial phase is complete, we verify there is no problems on injection, forming, tooling processes and secondary processing and approve tooling and part , When all parts are qualified, moving on to mass production of components.
Outputs |
![]() |
|
Initial MP On-Site supporting | At initial productions, various environmental and conditional change may cause initial failures to products. We will attend to initial factory productions to spot out any failures caused by mechanical issues and immediately work to perform improvements to ensure your first shipment of new product will be out on the world “defect-free”. |
Design Tools
![]() |
![]() |
![]() |
![]() |
![]() |
![]() |
![]() |
![]() |
Equipment and Facilities
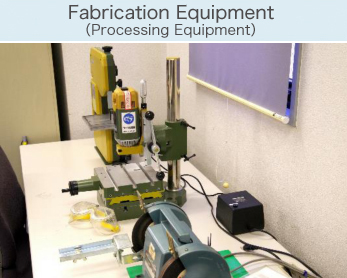
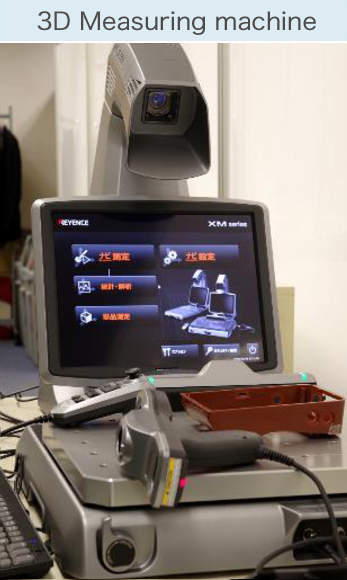